VWR Avantor
Warehouse Layout Optimization
The focus here is on the Academic project we ran for the client VWR, a subsidiary of Avantor. Working in a team of 8, we were tasked with improving the storage conditions in the warehouse by formulating a set of recommendations to 1. clear out the pallets sitting in the aisles, 2. identifying more cost efficient oreder policies, 3. creating up to 600 new pallet positions, the most important outcome.

What We Did
In a period of 3 months, we established an efficient dead stock removal policy to be strictly enforced on existing and future inventory, a new order policy allowing for considerable reduction in picks per day in the warehouse, and a redesigned warehouse layout offering additional pallet positions.
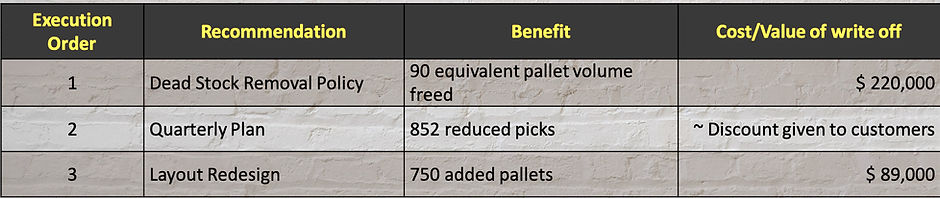
Deadstock Removal
Creating a Deadstock Policy Allowing for Reasonable Turnover and Space Liberation
We carefully analyzed the datasets of current and historical stock held in the warehouse, per region of the warehouse. Our analysis concluded that at a high level, there was considerable dead stock both in the raw material portion of the warehouse and in the finished goods warehouse. Applying the logic we developed in the table below, it was possible to free up 90 pallet positions readily and, in the future, this will guarantee less congestion in the warehouse due to obsolete items that will not generate profit in the long run.

Quarterly Ordering Policy
An Opportunity for Improved Operations
By Incentivizing the customers to order in bulk instead of placing small order quantities, the operating cost of the warehouse and the logistics costs could go down significantly. Our data analysis for the dead stock removal gave us a valuable insight with respect to the operational inefficiencies that the warehouse presented, in terms of picking and ordering quantities received, which are highly connected. We observed that more than 3/4 of order lines (~20% of Inv. Value) had order qty. ≤ 10. We isolated the customer-SKU pairs that were ordered more than once a month, and out of those we grouped those customer-SKU pairs with order qty. < mean & mode of the overall order quantity for selected SKU. The resulting groups were given the option of moving to a new quarterly ordering plan that would achieve the same service level and give them a commercial incentive. To make sure customers would not retract, this was recommended to be given as a recommendation but not as a contractual obligation on old contracts. The new order plan would be calculated as follows: [ Avg. monthly order frequency (per Cust-SKU) ∗ 3 months ∗ Avg. monthly order qty (per SKU) ].
This new policy gives the opportunity to generate a reduction of almost 40% of the total yearly orders.
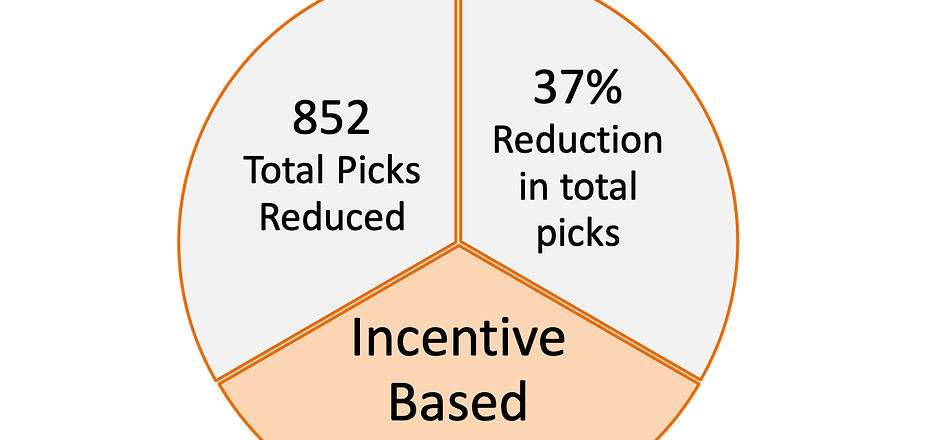

Layout Redesign
Numerous Proposed Layout Changes to Generate New Pallet Positions
We worked in detail using CAD drawings of the warehouse plan to find additional pallet positions, even in creative ways. In our detailed report, we explained the feasibility of the various recommended implementations. The current state of the warehouse when we started working offered manny challenges: clogged aisles,staged pallets on the finished goods warehouse for lack of space, incomplete registration of pallet locations in the WMS, as well as disorder and improper use of space in shelving areas for small products. The plan above was the current state of the layout before our work. Below you will see a series of layout changes and the relevant explanation. Each successive plan incorporates the recommended changes in the previous step.
The total sum of pallet positions created through these recommendations reached almost 700.